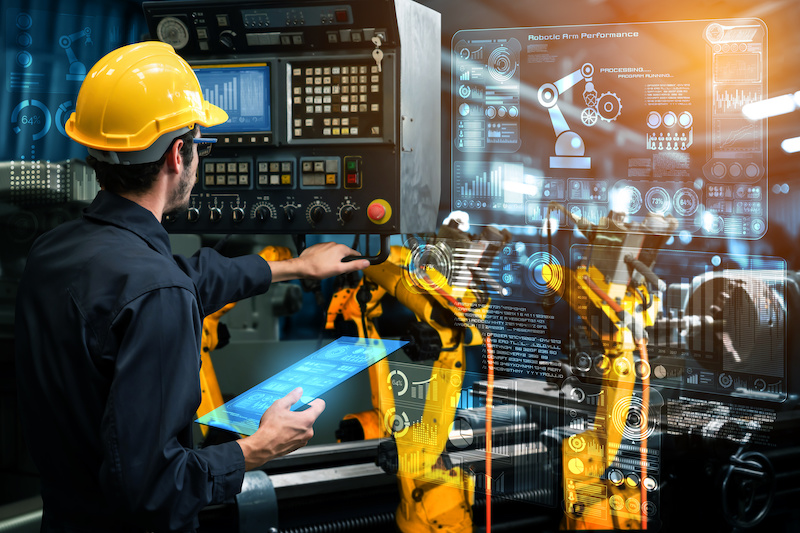
Need better power performance? Need to stop manual monitoring, or manual control of periodic operations? Need more data from your production floor? Then consider Industry 4.0 retrofitting from Mueller Electric
Your equipment may represent millions in capital expenditure and years of planning. Retrofitting your existing machines to improve or add new features such as always-on monitoring, data analytics, detecting defective products, or predictive maintenance may be the only answer. Mueller Electric offers Industry 4.0 retrofitting to help you achieve a new standard!
The IIoT (Industrial Internet of Things) helps to streamline manufacturing and provide information of a machine’s production volume, overall equipment efficiency (OEE), and optimization of power and production downtime. IIoT enables production flow monitoring, industrial automation, energy efficiency, and process monitoring. This is what retrofitting to the Industry 4.0 standard can mean for your manufacturing floor.
Industry 4.0 retrofitting is important for today’s industrial plant with improving features of the machine for performance and safety.  Retrofitting your equipment may be a solution for necessary upgrades compared to alternative large transformations and spending of capital upfront.Â
Mueller Electric creates the ability to focus on precise results. One smaller upgrade can lead to another, and another which in turn allows plant managers and operators to slowly adapt their production floors to become more Industry 4.0 and smart factory-oriented through increments. Whether you’re wanting to boost productivity, enhance performance, or improve safety, Mueller Electric provides valuable guidance to help you make informed decisions about retrofitting your machinery to meet Industry 4.0 standards.
What to consider to retrofit your machinery
1. Do you use your production floor to run a lot of jobs continuously where part changeovers happen frequently? Do you and your team spend more time than you would like programming and setting up for jobs and making frequent changeovers? If these circumstances present significant constraints and unwanted downtime, then a retrofit of your machinery would be a good idea.
2. Do you use your production floor to run a lot of jobs continuously where part changeovers happen frequently? Do you and your team spend more time than you would like programming and setting up for jobs and making frequent changeovers? If these circumstances present significant constraints with unwanted downtime, then a retrofit would be a good idea
3. If you need different types of machine heads for running different jobs, perhaps you can outfit one or two of your existing machines so they can be equipped with interchangeable machine heads. For instance if you need to have a combination of machine heads, such as straight heads for heavy-duty metal cutting; contour heads for profiling and curved cutting; and 90-degree heads for angled cutting, then retrofitting a machine so that it can use all three types interchangeably would be ideal. If you work with more than one type of axis, you could also further outfit your machinery so that the axes are interchangeable along with the heads.
4. While the above example of when to retrofit with metal cutting may be a given, there are other times when the idea of retrofitting equipment sounds good in theory, although when you take into consideration the time and money needed to do so the idea may not pan out as perfectly as you would want. For instance, in a case where you are looking to get data information from an older piece of equipment for predictive analytics where the only place it can be seen is on a human-machine interface, having a custom-made device specially crafted for the sole purpose of being able to externally access data may be very costly. While connecting your equipment to IIoT systems has limitless potential, some older pieces of equipment may be very difficult to digitize as they were never meant to function in this way. In cases like these, the investment may not be worth what you’re trying to accomplish.
Let’s say you have a possible need for retrofitting equipment but are unsure of the next steps to take. When considering doing a retrofit, you always want to create a specific goal that is as detailed as possible. For example, perhaps you and your staff are experiencing problems where production repeatedly gets bottlenecked in a certain area on your floor. What are your pain points? What could be done to improve the situation? This could be a good case for how retrofitting a piece of machinery could improve the situation.
In addition to pain points, other questions to ask yourself when contemplating a retrofit of your machinery include the following:
5. What are you trying to achieve?
6. What is your current situation?
7. What do you need in order to achieve the desired outcome?
After clearly assessing your needs, you can then form a business plan and even more detailed information on how a retrofit would be good for you and your company. How much time, money and products are lost by staff needing to clear bottlenecks that could be applied toward more seamless production? Any possible retrofit case needs to be backed by a careful cost analysis of how much money is being lost due to the current situation, how much the projected cost estimate would be to implement changes with a retrofit and how much money you would have to gain as an ROI over the course of one month, 6 months and a year after successful implementation.
Regardless of whether you plan to retrofit your equipment, go for a complete upgrade or keep your machinery as is, Mueller Electric is here to support you in your factory automation, Industry 4.0 retrofitting efforts. Contact us today for more information.