There’s no doubt you’ve heard about Industry 4.0 and that it’s explained as all the rage, but what is it really? And how can it help your manufacturing process? Read on to find out …Â
What is Industry 4.0? Industry 4.0 is a broad concept that refers to the fourth industrial revolution (the first Industrial Revolution being the Age of Mechanical Production in the late 18th century, followed by the Age of Science and Mass Production in the mid 19th century and the Digital Revolution that started in the mid 20th century) which expands on the most recent Digital Revolution by taking what has been computerized a step further and adding on interconnectivity as it applies to manufacturing and how society is changing to adapt to it. We’ve seen Industry 4.0 in manufacturing take place in the past decade and really take off in the past two years due to labor shortages and disruption caused by the effects of the COVID-19 pandemic.
Terms such as the Industrial Internet of Things (IIoT) and smart factories are more specific terms used under the umbrella phrase, Industry 4.0, that further describe types of technology and applications used in the fourth Industrial Revolution.
In manufacturing IIoT refers to the connecting and converging of technology applications, specifically that of machines, computers and digital technology, all for the purpose of enhancing industrial processes in order to become more efficient. For example, one IIoT application is predictive maintenance, or the use of sensors to stream data about machine activity, which can alert plant staff about current production conditions, possible warning signs and machine problems. It can even prompt routine maintenance checks. This can typically be done through devices, either on-site or through cloud-based applications, allowing staff to remotely control what happens on the production floor. Valuable benefits of predictive maintenance are endless and include controlling quality, adopting sustainability, tracing products, vastly reducing operational costs and keeping production equipment running smoothly and effectively … all of which are used in modern, smart factory practices.
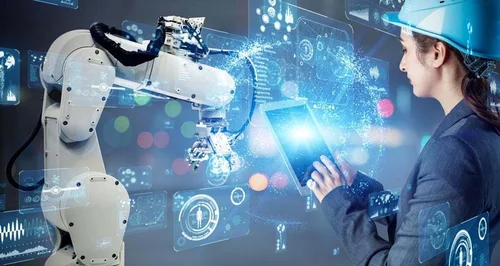
Process control systems such as SCADA, DCS or PLC systems are different types of control systems used to regulate how production is managed. SCADA, or Supervisory Control And Data Acquisition systems, are complete, large-scale software-based systems used to collect data from ALL machinery, devices and inputs on the production floor, and can be used remotely to monitor and control devices. SCADAs allow operators a complete overview of processes and are usually data-driven systems. SCADA systems can fairly easily be modernized for IIoT systems by utilizing cloud-based technology to be able to control machinery remotely or access data analytics information.
A DCS, or Distributed Control System, is similar to a SCADA system in that it is a computerized system for a plant’s manufacturing processes, however; it differs in that it does not contain a centralized computer or control room but autonomous controllers throughout the system. The reason for this is if a processor fails it only effects one part of the plant’s process, whereas with a SCADA system all processes would be effected. A DCS is the system of choice to use in industries where safety critical or continuous processing is done.
In contrast to SCADAs or DCS, Programmable Logic Controllers (or PLCs) are simpler and smaller systems used to control equipment in an industrial facility. PLCs rely on hardware and simple programming to monitor inputs and outputs and make logic-based decisions for automated processes or machines. Where SCADA systems are data-driven systems, PLCs are driven by instantaneous changes. Often PLCs can and are incorporated into larger SCADA systems.
No matter what system you use—whether a SCADA, DCS or PLC system—no matter how high-tech or low-tech you think you may be, Mueller Electric can help you with your manufacturing needs by providing factory automation cables for your plant machinery. Factory automation cables are the filaments that connect all manufacturing equipment and provide ultimate communication between all devices, resulting in seamless connectivity for a streamlined production floor. Whether you need UL-listed cables or custom cable assemblies, Mueller Electric has just the solution for you.
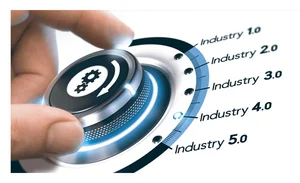
Feel free to browse our factory automation cable catalog and then contact Mueller Electric at 800.955.2629 for a free consultation on selecting the cables that best fit your application. We look forward to helping you with your factory automation needs!